Verdens første grønne betongfabrikk
Norske Cemonite har utviklet teknologi, som kan lage et bærekraftig alternativ til sement. Dette skal gjøres med å resirkulere eksisterende avgangsmasse fra gruver, og redusere energibehovet i produksjonsprosessen.
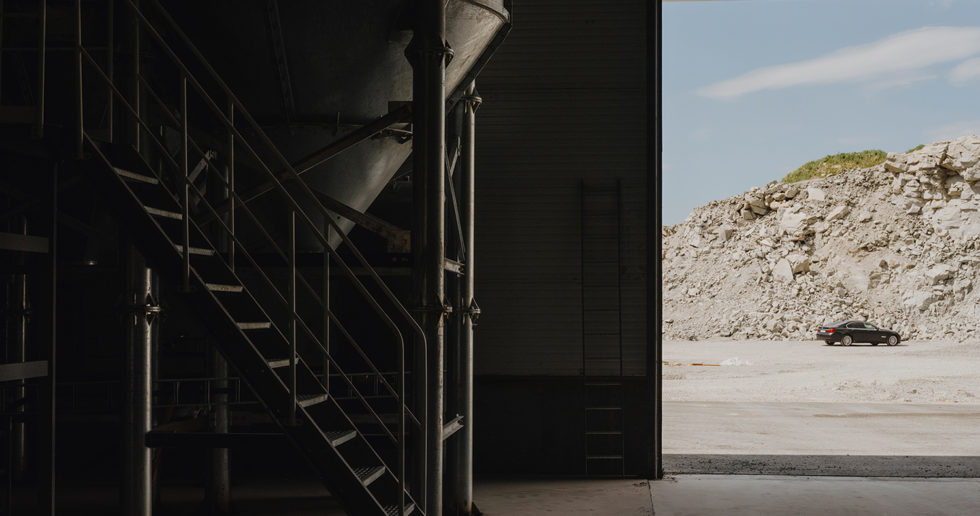
Sement-anlegget i Sandnes er digitalisert og delvis automatisert med systemer for elektrisk distribusjon og industriell automasjon fra Schneider Electric Foto: Oioioi
I pilotanlegget i Sandnes som ble åpnet i september i år, er det installert automatiseringssystemer fra Schneider Electric.
CEO Espen Lea i Cemonite forteller at de skal bruke pilotfabrikken til å demonstrere teknologien til potensielle kunder og samarbeidspartnere, for å utvikle, teste, lære og finjustere produksjonsprosessen før den blir fullskala.
– I tillegg til å løse en stor utfordring for gruveselskapene med å gjøre avgangsmassen til en ressurs, regner vi med at CO2-utslippene knyttet til sementproduksjon blir redusert med 80 prosent.
– Med tanke på at dette utgjør åtte prosent av verdens karbonutslipp, har vårt konsept stor betydning for industri og samfunn både i Norge og globalt. Lykkes vi med prosjektet, kan teknologien ha et stort eksportpotensial.
Løse miljøutfordringer
Pilotanlegget, som er digitalisert og delvis automatisert med systemer for elektrisk distribusjon og industriell automasjon fra Schneider Electric, skal etter hvert erstattes av en heldigitalisert fullskala-fabrikk som etter planen blir fullautomatisert.
Yngvar Ødegaard, direktør for industriell automasjon i Schneider Electric, er glad for at selskapet kan bidra til å løse miljøutfordringene med sementproduksjon.
– Det blir stadig strengere krav til bærekraftrapportering. Her er det viktig å ha full kontroll på prosessene og gode data. Det gjøres best med digitalisering, og bruk av teknologi som kanskje ikke er så vanlig i et produksjonsmiljø. Det gjør det også mulig å optimalisere prosessen for å minimere energiforbruket.
Fleksibelt anlegg
– Med tanke på at et industrielt pilotanlegg er i stadig utvikling, har det vært viktig med en teknisk løsning og programvare som er enkel å tilpasse underveis. Løsningen har derfor en høy grad av fleksibilitet, samtidig som programvaren er utviklet etter de nyeste standardene for kommunikasjon med åpne protokoller. Med å analysere sensordata kan produksjonen fortløpende optimaliseres.
– Systemet kan enkelt skaleres opp når fullskala-fabrikken skal bygges. Dette prosjektet har teknologi med et stort eksportpotensial. Samtidig tar vi med oss læring inn i andre prosjekter vi har globalt, for å være med på å akselerere overgangen til det grønne skiftet.
Høyest mulig oppetid
Lea forteller at de valgte Schneider Electric som teknologipartner fordi Cemonite er opptatt av å bygge et stabilt og sikkert produksjonsanlegg med høyest mulig oppetid, der måling og overvåking er sentralt.
– Målsettingen er best mulig sporbarhet i hele prosessen, god dokumentasjon og høy driftseffektivitet med bruk av minst mulig energi og ressurser. Oppstår det en feil i produksjonen, skal denne oppdages og rettes fortløpende.